BIG ASS FANS
Role
SENIOR PRODUCT DESIGNER
Duration
3 YEARS
Project
BEST IN CLASS LCD RESISTIVE TOUCH INDUSTRIAL CONTROL

THE DETAILS.
The BAFCon or Big Ass Fans Controller was the company’s first ever touch screen controller. BAF is the leading player in the industrial fan market with over 70% of the market share.
Competitors had more recently started using touch screens to modernize the control experience. Most were still using simple analog controls.
BAF sought to find the right balance of luxury and ruggedness our customers had come to expect while providing them with a thorough set of modern features to increase the value received.
Cross Functional Partners.
For this project I partnered with a junior designer on the team as well as a combination of physical and digital product owners, product marketing team members, and engineers. We frequently consulted with Support Team members as well.

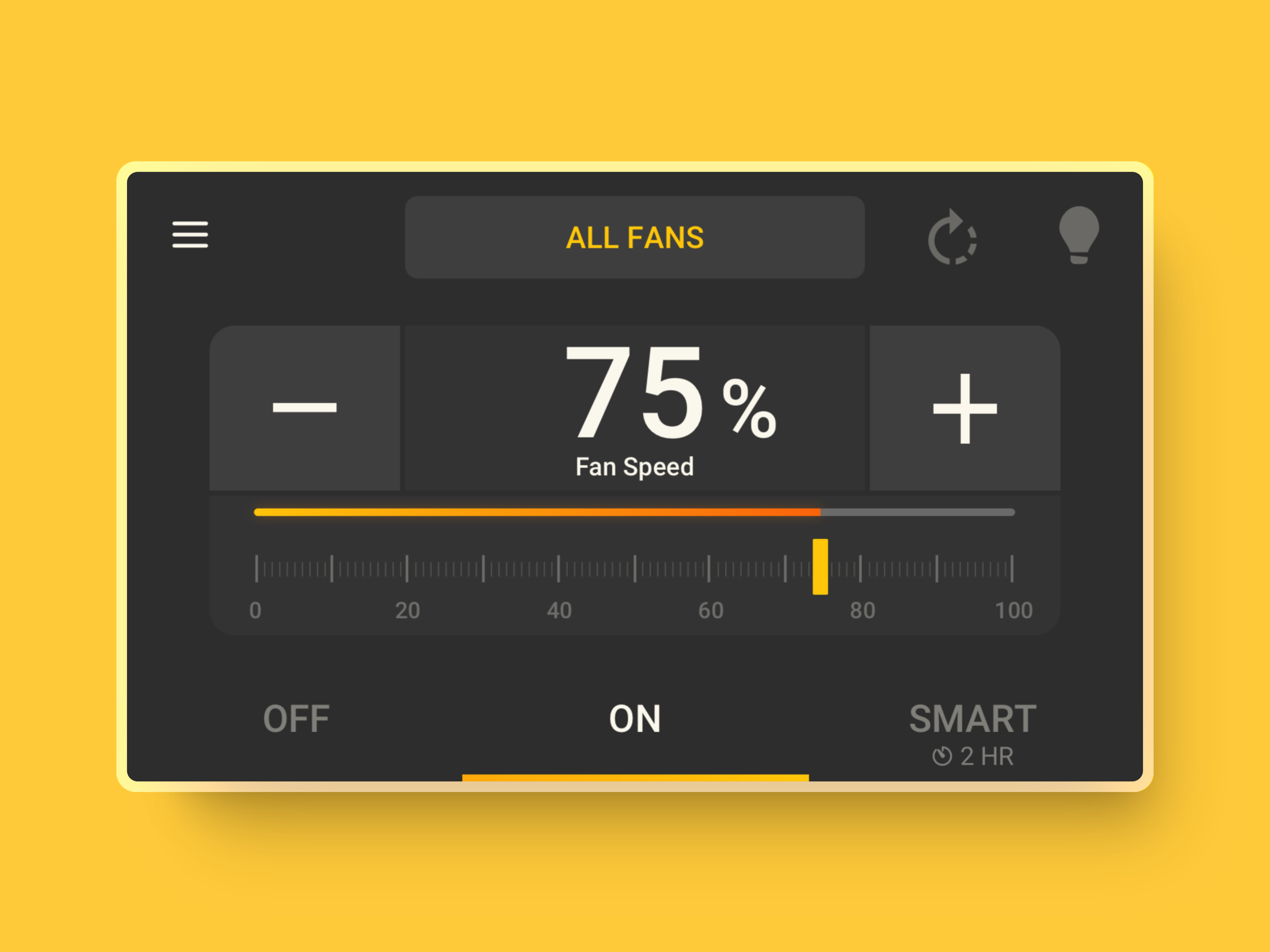

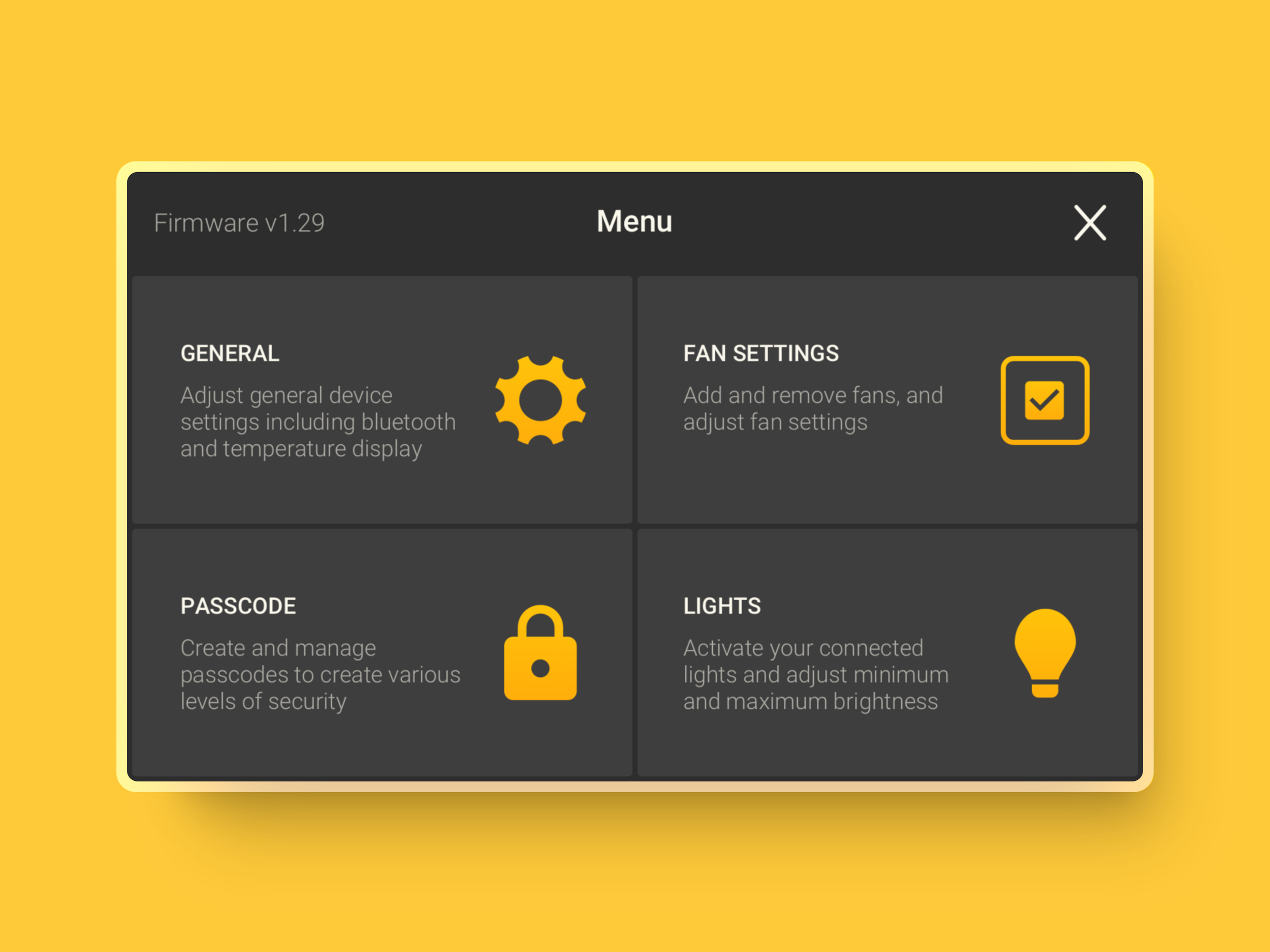
END RESULT.
The final product was a market leading jump in technology not provided by any of BAF’s competitors. Big Ass Fans was the leading brand in industrial fans and would further cement that lead by bringing the most advanced control systems to market. Our touch screen device and the systems we continued to build off of this success paved the way for that innovation.

PAIN POINTS.
To identify pain points we scheduled in-person interviews with customers from around the region. Big Ass Fans is lucky to have a large fan base and it well supported as a brand. It was easy for us to reach out to customers and schedule time to walk through their facilities.
With each interview we had the customer walk through how they use their product and logged what sort of control they had in place at the time. We frequently found that customers had come up with inventive ways circumvent inappropriate use of the fan controls either by employees or customers.
CONCEPT AN MVP.
After the team was armed with enough information to get started we took our findings back to HQ and presented them to the broader product team. We ran two design sprints to iterate on the ideal flows and features for our MVP. We settled on the base flow seen in the image above. It consisted of some basic controls that could operate on a one to many pattern. We were also able to include smart (auto) technology, some basic settings, light controls, and most importantly troubleshooting.
One of the best things we delivered with this product was the self sufficiency provided by the readable screen to let users try and troubleshoot their own issues. In the past these analog controls could only show sequences blinking lights that had to be matched to a book of error codes. Alternatively it would require a call to customer support.
DESIGN BASIC PROTOTYPE.
The prototype we created was extensive and worked well enough on an iPad to allow us to perform return visits to regional customers in order to collect scenario based feedback on the new prototype.
This feedback was extremely valuable in deciding on our final user flows.
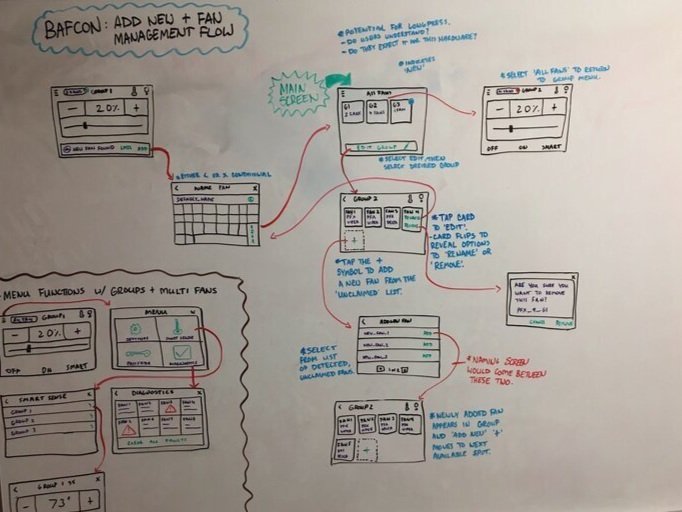
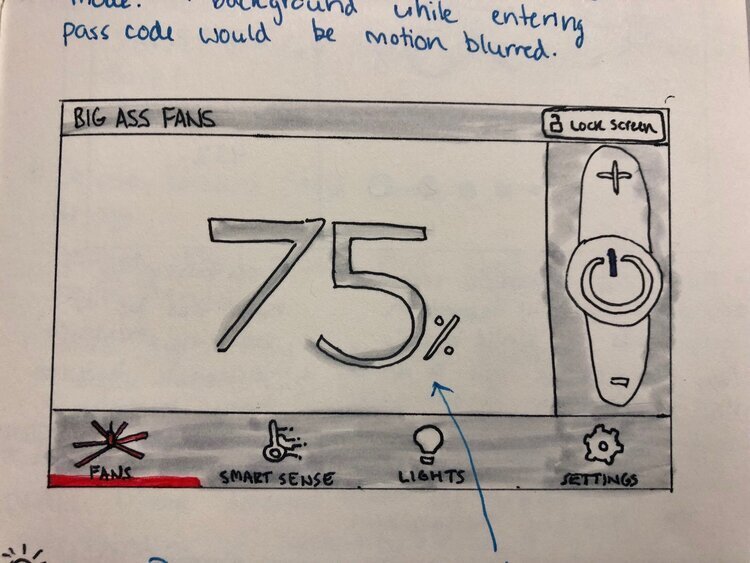
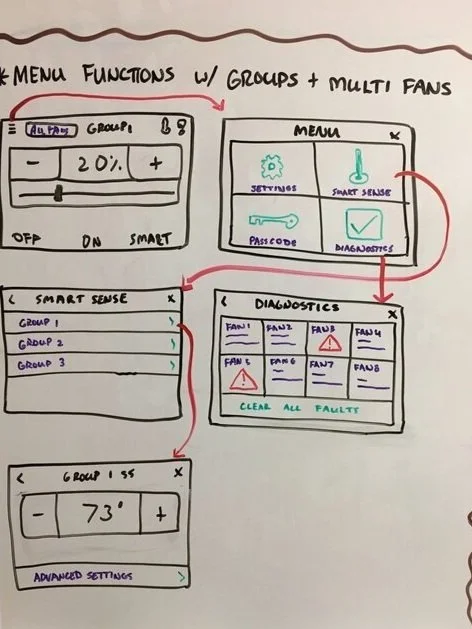
WHAT WE LEARNED.
Results.
This product is my single biggest success. I feel like I’ve created plenty of interesting and easy to use products over the years. But this one alone provided the best return on value to my company. It was an absolute success and I’m proud of the work we did.
Next Steps.
Over the course of the next 2 years post launch I supported this product by adding:
A design system to support future designers approaching the product.
Motion Controls
Multi-Fan Controls
Fan Grouping
Improved Smart Sense
Improved Diagnostics
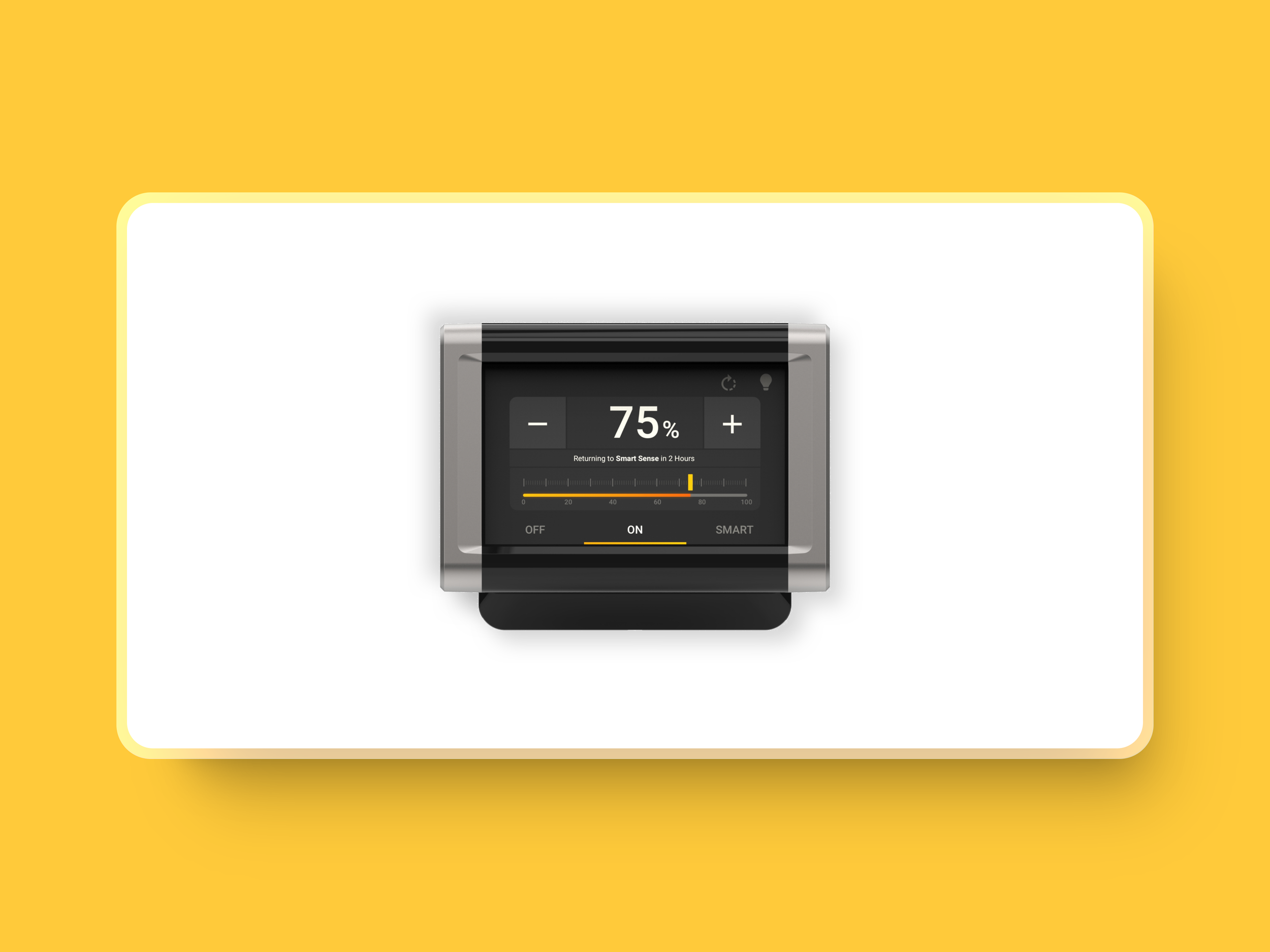

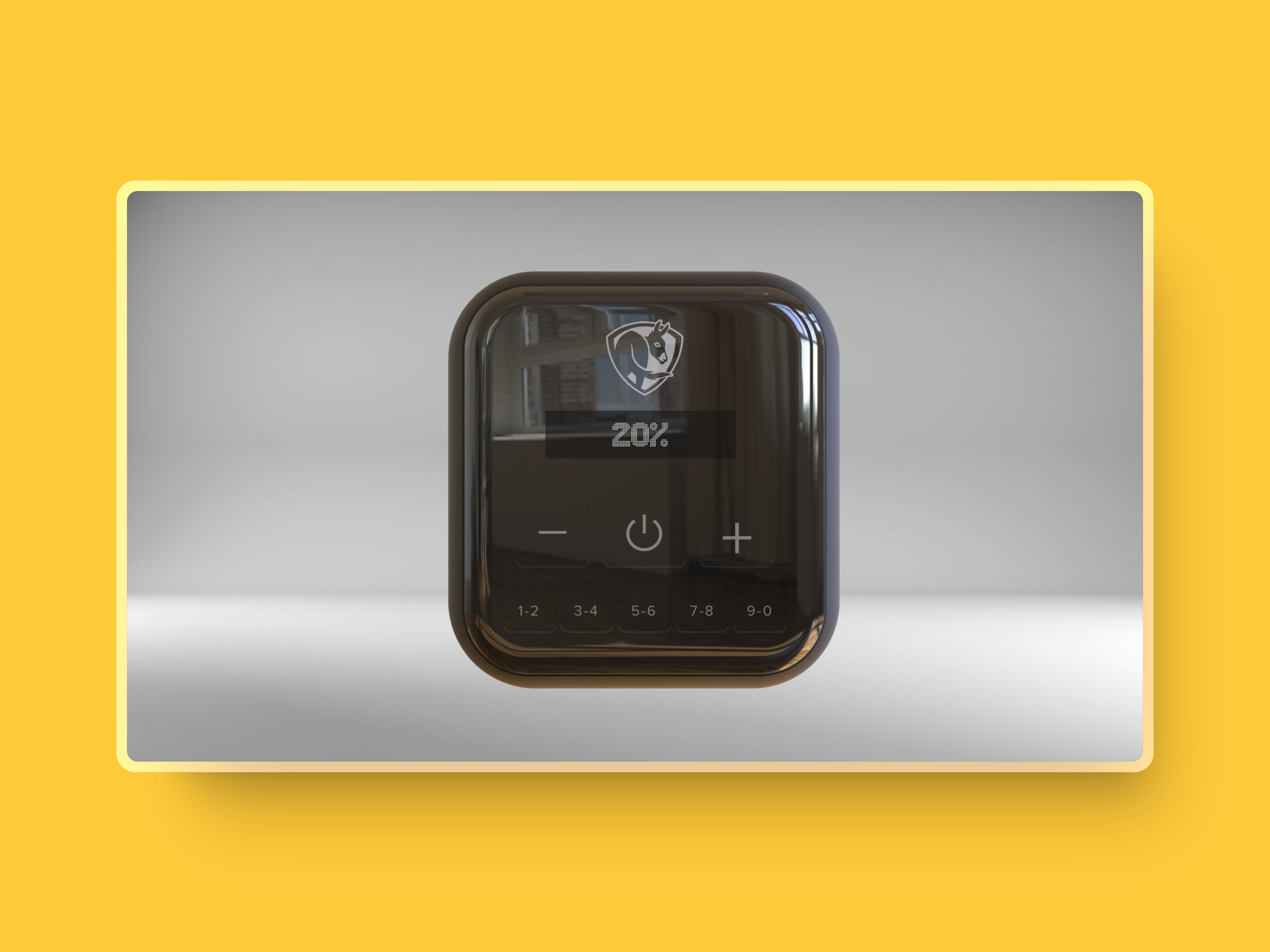

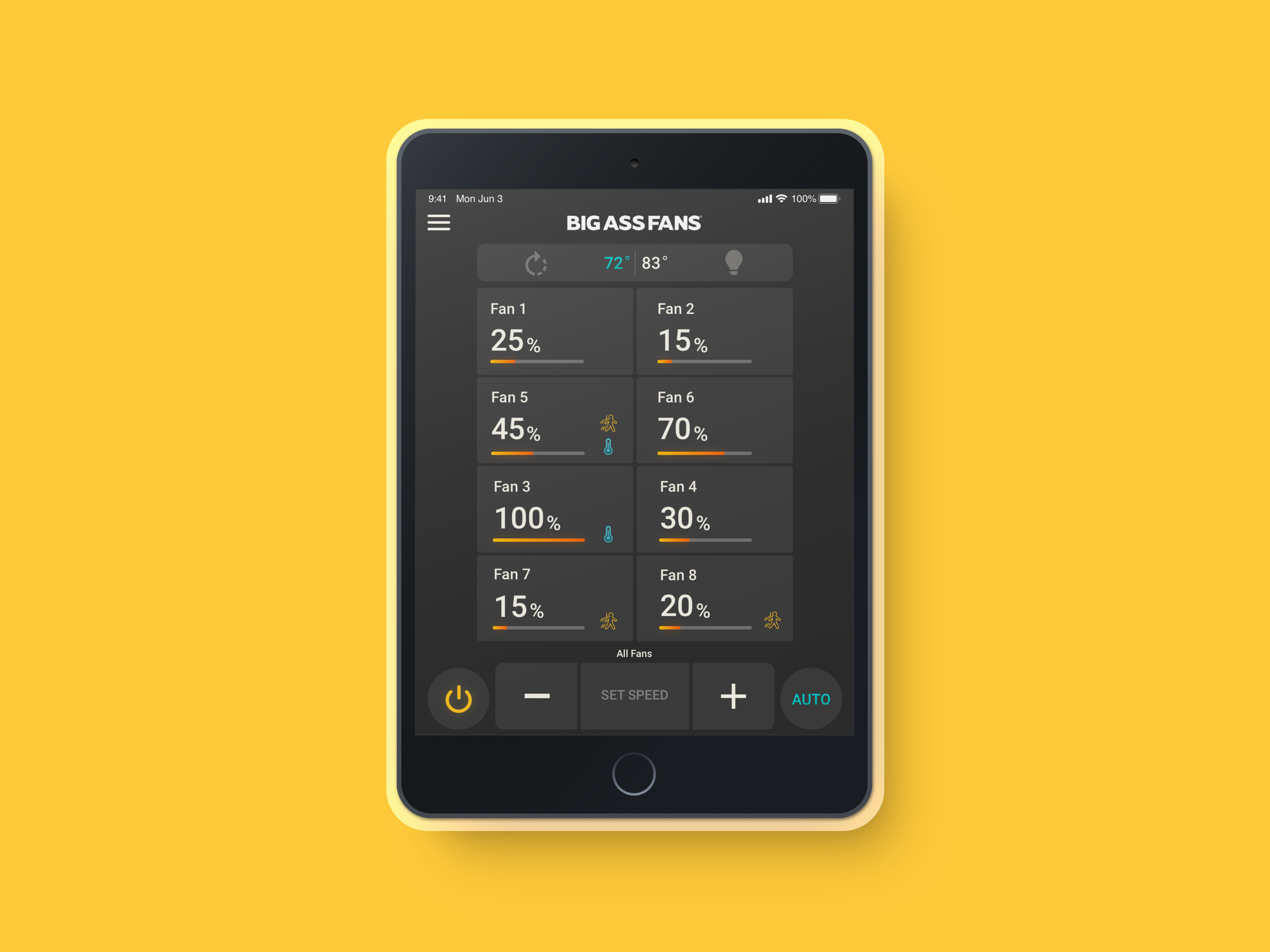
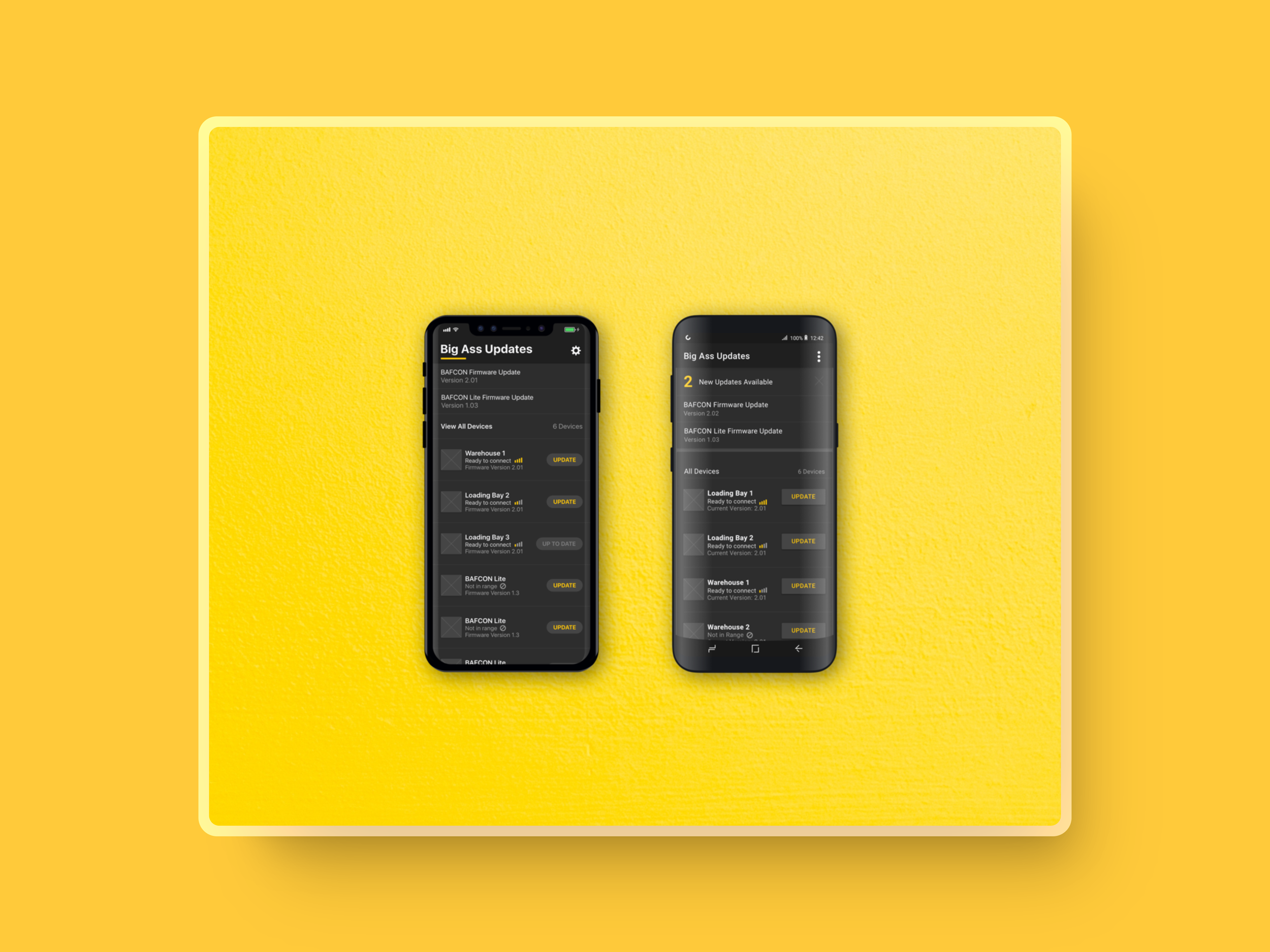



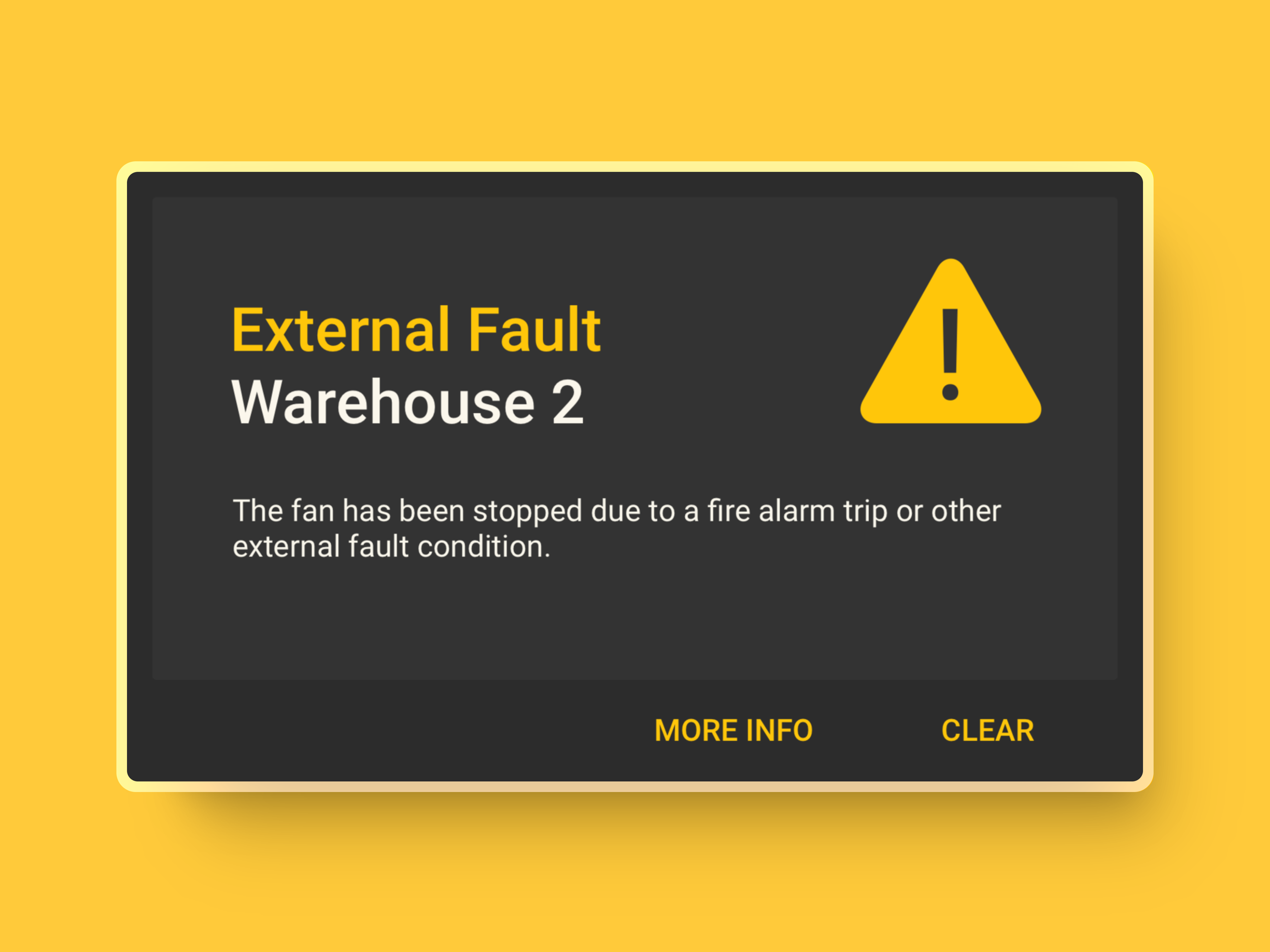
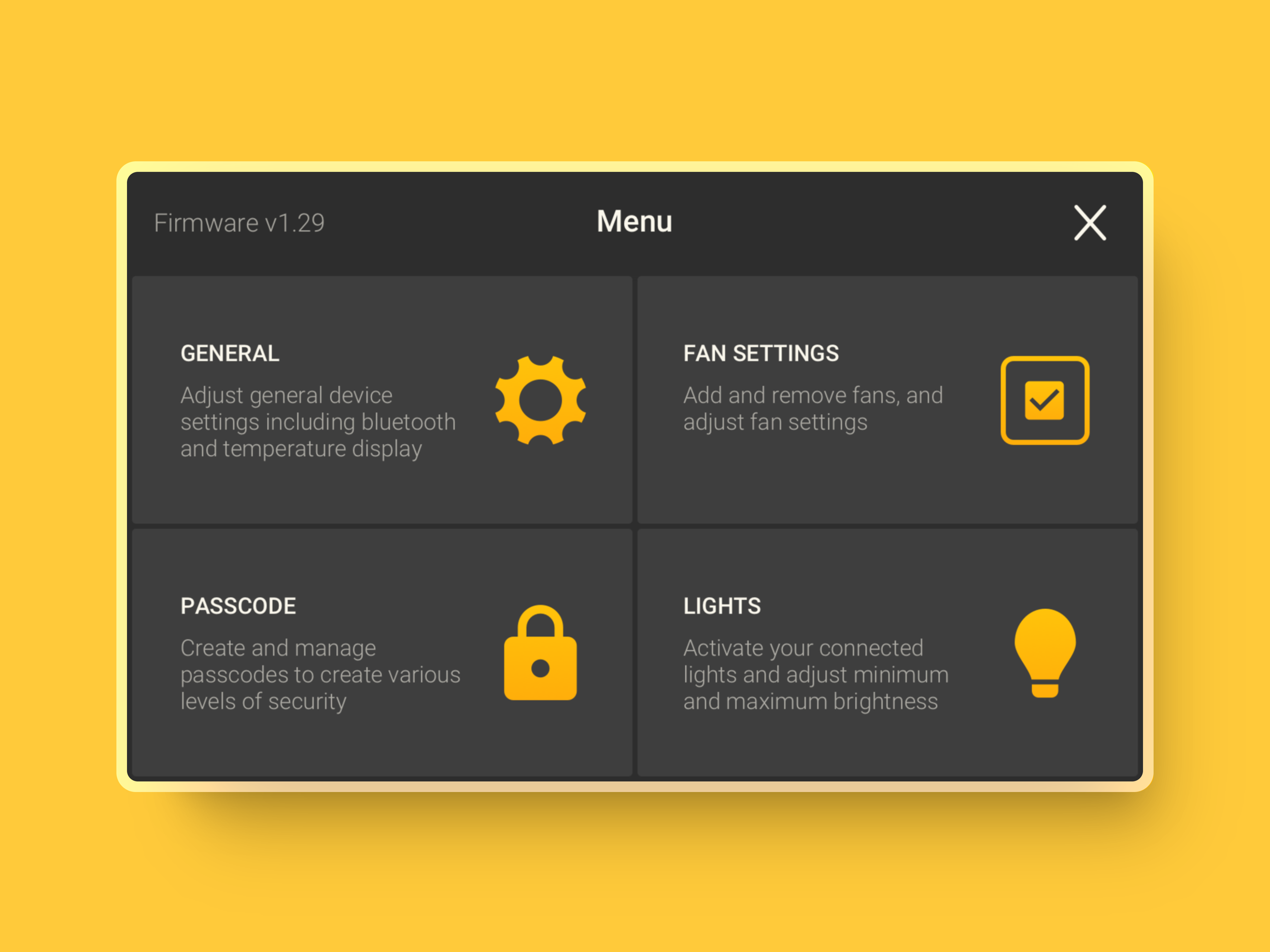
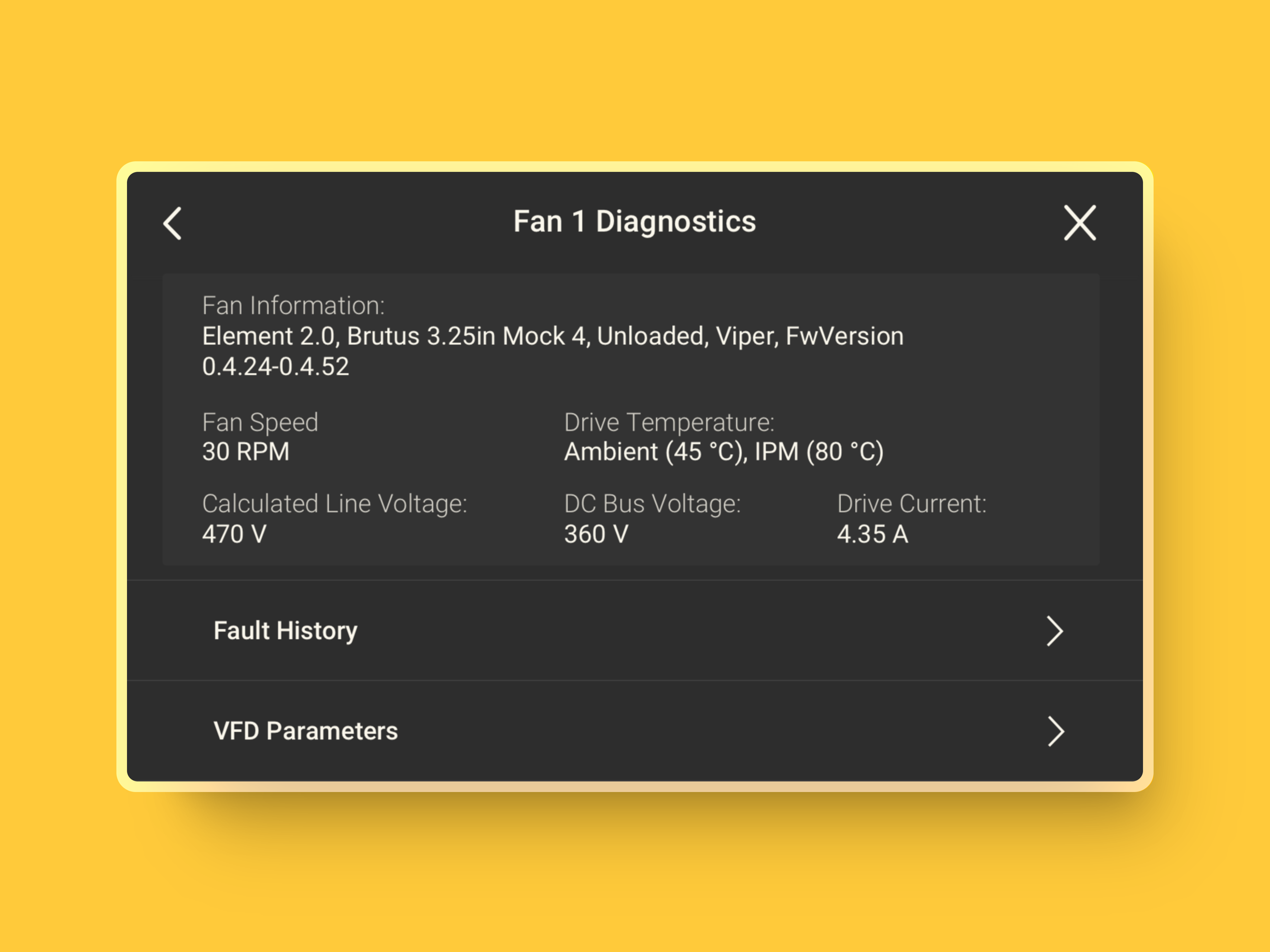